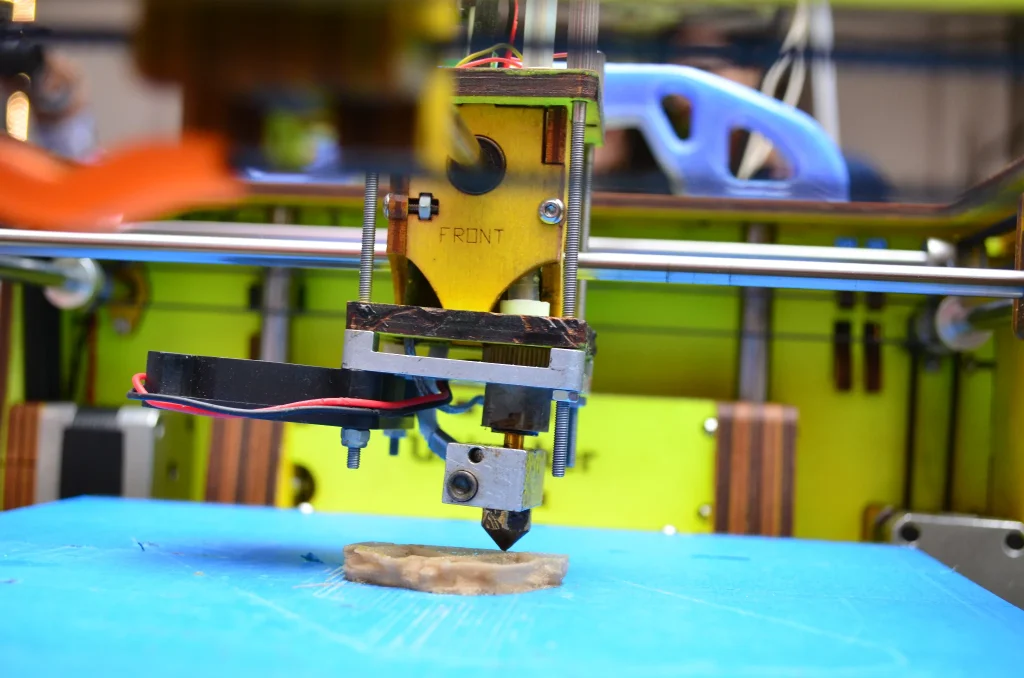
The Confluence of Additive and Subtractive Manufacturing Technologies
The manufacturing sector is undergoing a paradigm shift through the synergistic integration of two transformative technologies: additive manufacturing (3D printing) and subtractive laser cutting. While each technology demonstrates distinct advantages in isolation, their convergence unlocks unprecedented capabilities that transcend conventional production limitations.
This technical analysis examines the compatibility and operational synergies between these systems, addressing the critical question:Â “Can laser cutting systems achieve seamless integration with 3D printing technology to create hybrid manufacturing platforms?”
Technical Deconstruction: Operational Mechanisms
A fundamental understanding of both technologies is essential to evaluate their integration potential.
1. Additive Manufacturing (3D Printing)
- Process Fundamentals: Layer-by-layer material deposition via computer numerical control (CNC), utilizing thermoplastic polymers, metal powders, or composite resins.
- Key Methodologies:
- Fused Deposition Modeling (FDM): Thermal extrusion of thermoplastic filaments through a precision nozzle (X/Y/Z-axis control).
- Selective Laser Sintering (SLS): Powder bed fusion using high-power lasers for metallic/composite parts.
- Advantages:
- Geometric complexity beyond traditional machining constraints.
- Rapid prototyping and on-demand production capabilities.
2. Subtractive Laser Cutting
- Process Fundamentals: Non-contact material ablation via focused laser beams (COâ‚‚/fiber lasers), optimized for 2D/2.5D machining.
- Operational Parameters:
- Wavelength-dependent material interaction (absorption spectra).
- CNC-guided beam positioning (µm-level precision).
- Advantages:
- High-speed processing with superior edge quality.
- Multi-material compatibility (metals, polymers, ceramics).
Hybrid System Architecture
The integration of these technologies manifests through two primary configurations:
-
Sequential Hybrid Processing
- Workflow:
- Additive manufacturing constructs near-net-shape components.
- Laser cutting performs precision edge finishing, surface texturing, or functional feature generation.
- Technical Benefits:
- Combines geometric freedom with micron-level accuracy.
- Enables functional grading (e.g., porous structures with precision fluid channels).
-
Concurrent Hybrid Systems
- Integrated Machine Platforms: Coaxial integration of deposition nozzles and laser optics within a single CNC framework.
- Capabilities:
- Real-time alternation between additive and subtractive operations.
- Closed-loop thermal management for process stability.
Technical Advantages of Hybridization
Parameter | Additive Manufacturing | Laser Cutting | Hybrid System |
---|---|---|---|
Dimensional Accuracy | ±100-200 µm | ±10-50 µm | ±20-50 µm |
Surface Finish | Ra 10-25 µm | Ra 0.8-3.2 µm | Ra 1.6-6.3 µm |
Production Speed | Moderate | High | Optimized |
Design Complexity | Unlimited | Planar | Enhanced |
Key Benefits:
- Enhanced Metrology: Laser profilometry enables in-process quality validation.
- Material Efficiency: Net-shape additive construction minimizes subtractive waste.
- Functional Integration: Embedded electronics/fluidics via precision laser micromachining.
Industrial Applications
1. Medical Device Manufacturing
- Patient-Specific Implants: Titanium lattice structures with laser-polished articulation surfaces.
- Surgical Tools: 3D-printed ergonomic handles with laser-cut retention features.
2. Aerospace & Automotive
- Lightweight Components: Topologically optimized brackets with laser-drilled cooling channels.
- Conformal Cooling Systems: Additively manufactured injection molds with laser-smoothed cavities.
3. Advanced Electronics
- Embedded Sensors: 3D-printed housings with laser-ablated conductive traces.
Technical Challenges & Mitigation Strategies
Challenge | Solution Approach |
---|---|
Thermal Interference | Active cooling systems + process sequencing algorithms |
Material Compatibility | Development of hybrid-optimized alloys/polymers |
System Calibration | Multi-sensor feedback (LVDT, pyrometers) |
Software Integration | Unified CAM platforms (e.g., Siemens NX Hybrid) |
Future Outlook
Emerging developments indicate three critical trajectories:
-
AI-Driven Process Optimization: Machine learning for real-time parameter adjustment.
-
Multi-Material Hybridization: Simultaneous processing of dissimilar materials.
-
Nanoscale Integration: Combining laser micro/nano processing with additive nanomanufacturing.
Conclusion
The strategic convergence of 3D printing and laser cutting technologies represents a seminal advancement in advanced manufacturing systems. By transcending the inherent limitations of standalone processes, hybrid platforms deliver:
- Unprecedented design freedom
- Production efficiency gains
- Functional performance enhancements
As material science and digital twin technologies mature, this synergy will fundamentally redefine manufacturing capabilities across industrial sectors, validating the axiom that technological integration yields multiplicative rather than additive value.
“The future of manufacturing lies not in choosing between additive or subtractive methods, but in mastering their orchestration.”